Manufacturers, metalworkers, and engineers have many options for manufacturing processes, but Photochemical Etching (PCE) stands out. PCE is a chemical machining process that produces complex parts from sheet metal, such as stainless steel, aluminum, brass, etc. It involves using a chemical etchant to selectively remove material from the metal’s surface, allowing for parts with intricate shapes and tight tolerances.
However, PCE is one of many manufacturing processes available. Other processes include laser cutting, stamping, electro-discharge machining (EDM), waterjet cutting, and photo electroforming (PEF). We’ll briefly explain each process’s advantages and disadvantages, so you’ll understand why PCE is your best option
Advantages Of Using Laser Cutting
Laser cutting is a highly efficient and precise method of cutting materials used in many industries, such as automotive and aerospace. It requires less energy than other methods, can be automated using CNC systems, and produces exact replicas with minimal waste. It boasts numerous advantages over other processes, including:
-
- The ability to construct ultrahigh-precision components
- The ability to accurately replicate the outside shape of a piece
- PEF can be used with micro-PEF technology to use planar-surfaced substrates and photoresists with ultrahigh resolution
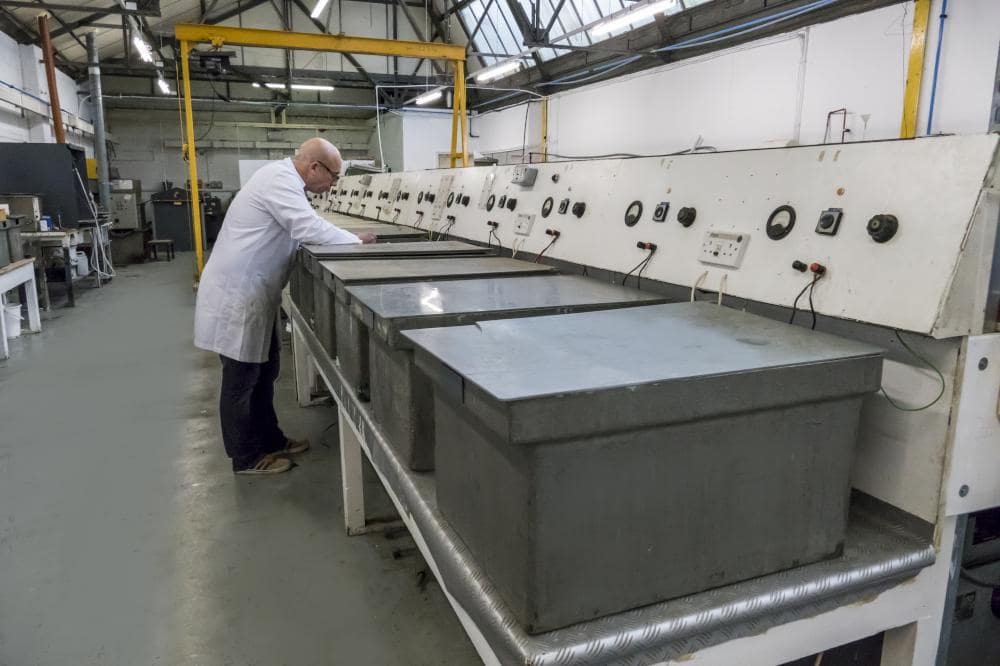
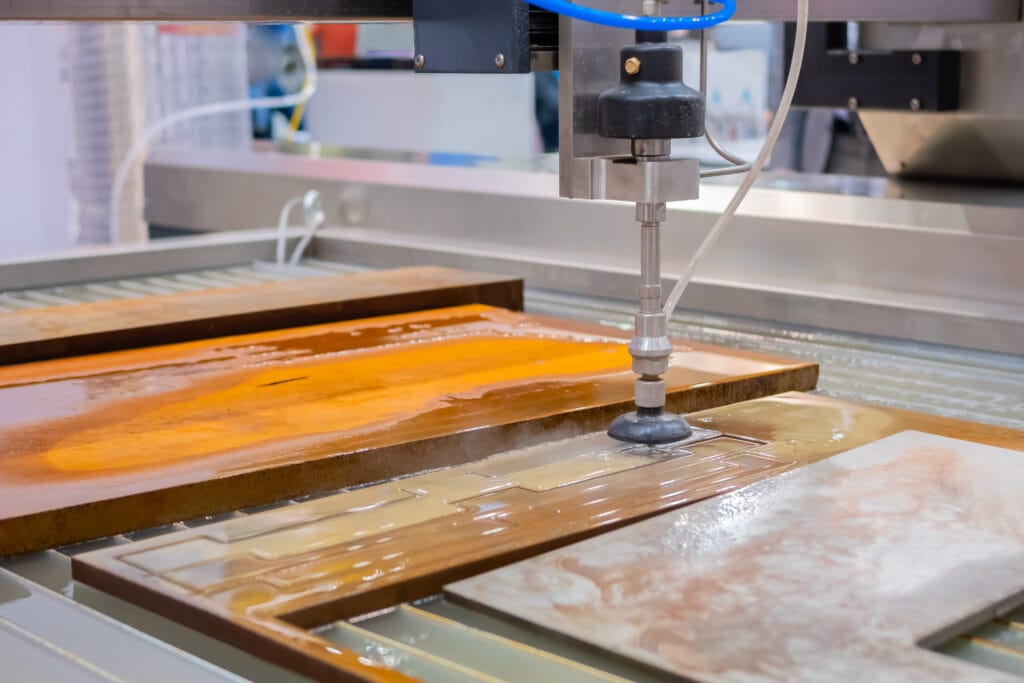
Disadvantages Of Photo Electroforming (PEF)
Photo electroforming (PEF), while an incredibly accurate method, produces small production runs relatively slowly compared to more traditional methods. Additionally, PEF’s drawbacks include the following:
- Slower turnaround time (typically five days)
- Somewhat more expensive than other methods
- It has some hardness restrictions that can factor into the finished material
- PEF also has poor throwing characteristics, meaning deposits produced on vertical surfaces may be uneven.
Please read The Top 5 Reasons to Use Photochemical Etching for additional information on why you should choose PCE for your following manufacturing process.
Additionally, refer to the chart to read the advantages and disadvantages of all the processes we provided in this article.

Finally, we’re happy to address any concerns or questions you may have on the PCE process. We’re experts at walking our customers through the entire process to ensure they’re satisfied every step of the way.
-
- It takes longer than traditional cutters for certain materials
- It’s challenging to create intricately detailed components due to its pressurized stream of water-eroding material
- Engraving is not its strong point