Explore some of the complex challenges faced in aerospace engineering and how precision machining is helping to drive innovation in this rapidly evolving field.
As technology advances at a rapid rate, we’ve continued to push the boundaries of exploration and innovation, propelling the aerospace industry to new heights, quite literally.
Every leap forward comes with complex challenges that engineers and manufacturers must overcome, from conditions and constraints to compliance. Aerospace engineering delivers challenges unlike any other industry.
To meet the rigorous demands of aerospace engineering and overcome these complex challenges, manufacturers turn to precision machining, especially photochemical etching, to provide high-quality, reliable aerospace components with exceptional precision and efficiency.
E-FAB specializes in precision machining for various industries, including aerospace engineering. Employing cutting-edge precision aerospace machining techniques, E-Fab produces components with superior accuracy and complexity.
In this article, we explore some of the complex challenges faced in aerospace engineering and how precision machining is helping to drive innovation in this rapidly evolving field.
The Extreme Conditions Faced by Aerospace Components
From the freezing temperatures of space to the scorching heat encountered during re-entry into the Earth’s atmosphere, aerospace vehicles operate in some of the harshest environments imaginable. To combat the challenging conditions, materials, and systems must be designed, manufactured, and tested to withstand such extremes while maintaining structural integrity.
The complexity of aerospace systems also demands precision in design, manufacturing, and assembly. Even the slightest deviation from specifications can potentially lead to catastrophic consequences, which is where the power of precision machining is most important.
Aerospace engineers can achieve exceptional accuracy and consistency in producing critical components by employing advancing manufacturing processes. Utilizing advanced processes allows for tight tolerances and fine surface finishes, ensuring optimal fit, functionality, and longevity of aerospace parts, even in extreme conditions like high temperature, vibration, and corrosion.
Photochemical etching has become a popular process within the aerospace industry due to its unique advantages, including the ability to fabricate intricate and complex geometries with tight tolerances precisely. The lightweight yet robust, thin metal parts produced by photochemical etching come from a wide range of materials, including stainless steel, titanium, and nickel alloys, which are well-suited for aerospace applications.
Photochemical etching allows you to create customized designs and features that enhance aerodynamic efficiency and structural integrity. Photochemically etched components also exhibit superior corrosion resistance and fatigue strength, essential for critical aerospace applications.
Weight Constraints in Aerospace Applications
In aerospace engineering, every ounce matters because a vehicle’s weight directly impacts its performance, fuel efficiency, and payload capacity. To solve this, engineers must constantly develop lightweight yet durable materials and components to maximize efficiency without compromising safety.
By utilizing lightweight materials such as advanced composites, titanium alloys, and aluminum-lithium alloys, aerospace vehicles can significantly reduce their overall weight without compromising structural integrity or safety. This reduction in weight translates directly into improved fuel efficiency, allowing for longer flight ranges, increased payload capacity, and reduced operational costs. These lightweight materials also contribute to enhanced maneuverability, agility, and speed, enabling aerospace vehicles to achieve superior performance and responsiveness.
Precision machining plays a pivotal role in the production of lightweight yet powerful aerospace components by enabling the application of intricate designs and the optimization of materials. Through advanced machining techniques, aerospace engineers can achieve precise control over material removal, creating lightweight structures with optimized strength-to-weight ratios.
Precision machining also allows for fabricating intricate designs and complex geometries that maximize structural integrity and performance while minimizing weight. This combination of material optimization and intricate design empowers aerospace manufacturers to produce components that are not only lightweight but also robust and powerful, essential for enhancing fuel efficiency, maneuverability, and overall performance in critical aerospace applications.
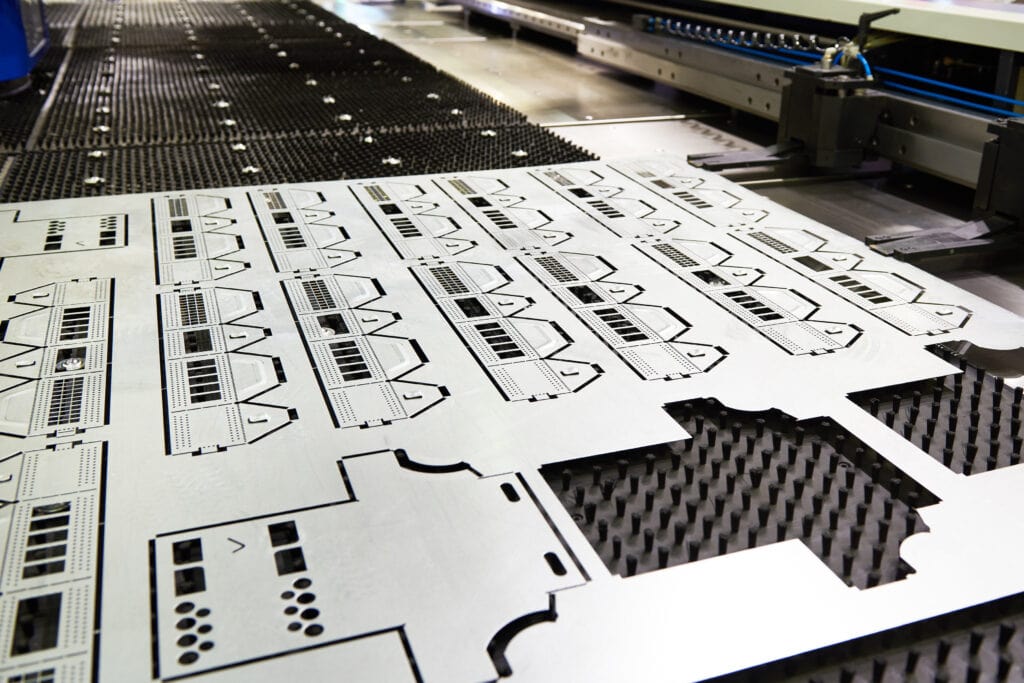
Complex Geometries in Aerospace Manufacturing
Driven by the need for optimal performance, efficiency, and safety, as well as specific aerodynamic, structural, and functional requirements, the demand for intricate shapes and designs in aerospace components is unlike any other industry, and this presents engineers with their own set of challenges.
From turbine blades with precisely engineered airfoil shapes to spacecraft components with intricate heat dissipation features, the ability to fabricate complex geometries is essential for a wide range of aerospace applications.
Proven metal manufacturing techniques such as precision aerospace CNC machining, 3D printing, and, most notably, photochemical etching have become essential in delivering the precise, intricate shapes and designs required to enhance the performance and efficiency of aerospace systems. Photochemical etching enables the delivery of intricate designs with superior accuracy and repeatability, which is why it’s become the trusted technique for manufacturers responsible for quality, reliable aerospace parts
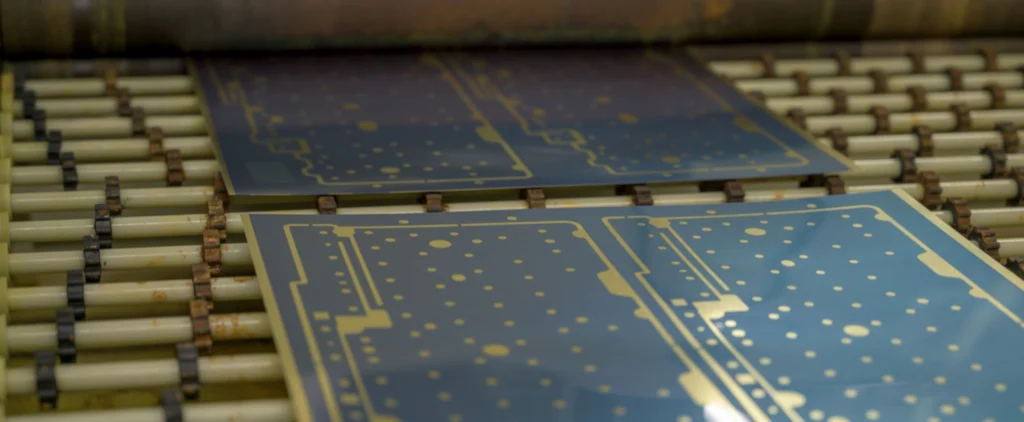
Advantages of Precision Machining for the Aerospace Industry
With its high accuracy and tight tolerance capabilities, precision machining ensures that aerospace components meet stringent specifications and requirements, which are crucial for the demanding environments encountered in flight. And the advantages don’t stop there.
Due to their high tolerance capabilities, proven precision techniques such as photochemical etching ensure that precision machined parts are manufactured with exceptional accuracy and consistency. These techniques can utilize a wide range of materials, from traditional metals like aluminum and steel to advanced alloys and composites, providing unmatched versatility in the production of complex and intricate components.
Whether through precision photochemical etching, or other machining processes, precision machining’s scalability is also a huge advantage. It allows for the production of components ranging from intricate small parts to large-scale structures while maintaining uniform quality and precision throughout the manufacturing process.
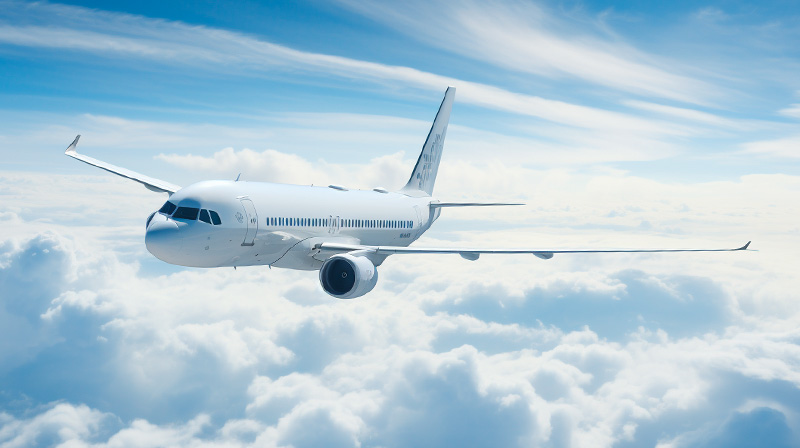
E-Fab's Expertise in Aerospace Precision Machining
Known for our experience, expertise, and experimentation, E-FAB blends innovation with compliance to develop intricate, precision components for aircraft, spacecraft, and aerospace technologies.
With a focus on collaboration, we work closely with aerospace clients throughout the project lifecycle to deliver customized, high-precision components tailored to the unique requirements of this critical industry.
Here’s what sets E-FAB apart:
Advanced Manufacturing Techniques
We use cutting-edge precision machining methods, including photochemical etching, to produce aerospace components with unparalleled accuracy and complexity. Our advanced machining process enables us to manufacture intricate geometries and achieve the tight tolerances demanded by aerospace applications.
Material Knowledge and Versatility
Aerospace engineering often requires working with a diverse range of materials, from lightweight alloys to high-strength composites. Our team has a deep understanding of the properties and behaviors of these materials so that we can optimize machining processes for each specific material and application.
Quality Assurance and Compliance
With rigorous quality control standards and an ISO9001:2015 certification, we ensure that every aerospace component meets or exceeds industry regulations and standards. Our commitment to quality assurance encompasses comprehensive inspection processes and adherence to the specific requirements of the aerospace industry.
Innovation and Problem-Solving
Our team of engineers and technicians are skilled problem solvers, adept at finding innovative solutions to the unique challenges encountered in aerospace manufacturing. Whether overcoming design complexities or optimizing manufacturing processes, we thrive on innovation to deliver cutting-edge solutions for aerospace clients.
Customer Collaboration and Support
Our engineers, manufacturers, and quality assurance specialists work hand in hand with aerospace customers to uncover boundary-pushing innovations beyond what many other manufacturing companies will attempt.
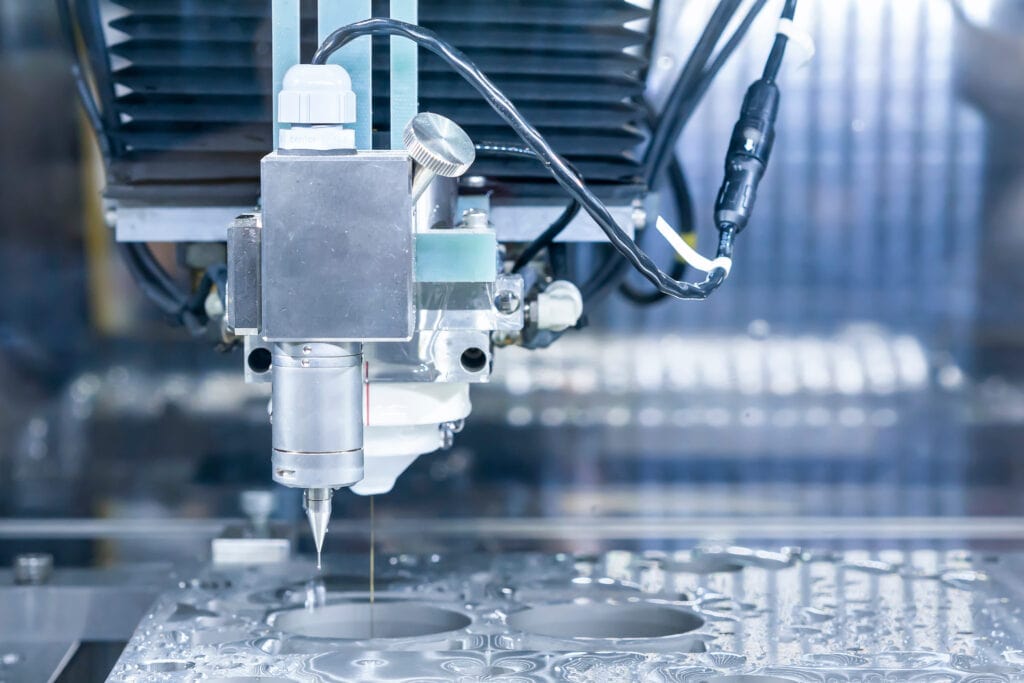
Precision Machining for Your Next Aerospace Project
When you work in aerospace engineering, you’re responsible for highly sensitive applications where failure is not an option. As the industry continues to evolve, precision machining is becoming more and more critical for meeting the rigorous demands of aerospace engineering and overcoming the complex challenges it provides.
Precision machining, especially photochemical etching, continues to be at the forefront of aerospace innovation, helping to take the industry to new heights by providing high-quality, reliable aerospace components with exceptional precision and efficiency.
With over 40 years of experience, E-FAB leads the way in precision etching, prototyping, and producing intricate parts essential for aerospace applications. Working with innovation at our core, we continually invest in state-of-the-art technology, including direct imaging printers, to provide accuracy and precision that can be relied on for even the most extreme applications.
When it comes to high-quality, complex components that will stand up in even the harshest aerospace conditions, you can rely on the team at E-FAB, your precision machining aerospace partner.