With its high precision and efficiency, photochemical etching is quickly becoming the preferred process for industries that require accuracy and quality.
Offering a number of advantages over traditional metal fabrication techniques, photochemical etching is ideal for producing parts with high-precision tolerances and complex geometries for a range of industries, from aerospace and medical, right through to electronics and defense.
But there is much more to photochemical etching than its superior accuracy, greater design flexibility, and reduced material waste. In this article, we look at what exactly photochemical etching is, its process, applications and advantages.
What is photochemical etching?
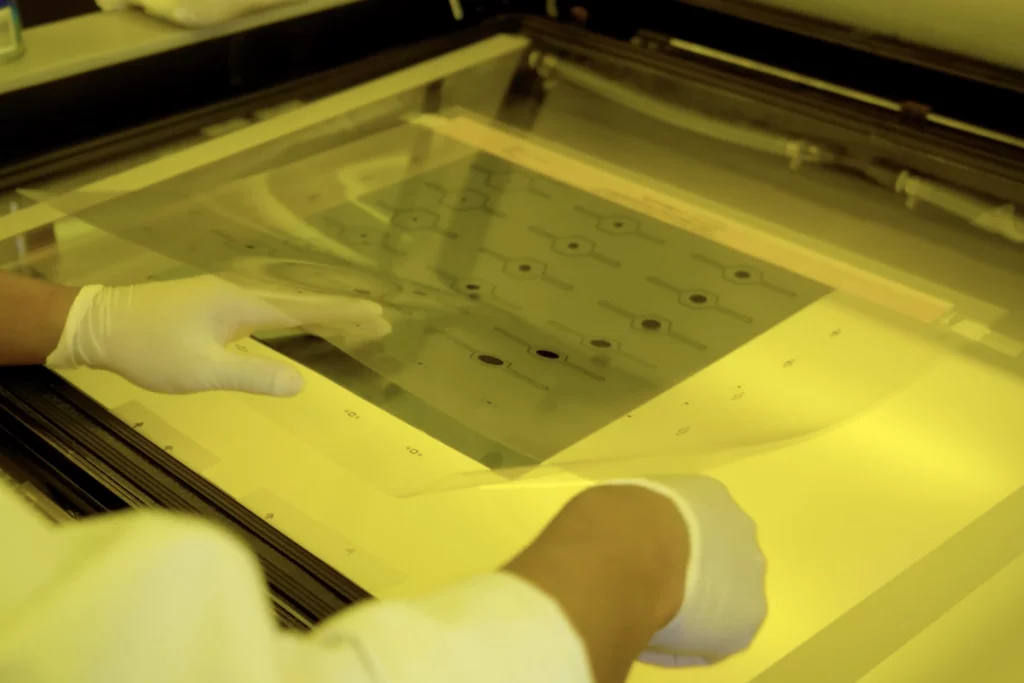
Also known as photochemical machining (PCM) or metal etching, either photochemical milling or photo etching is a highly precise, cost-effective metal machining process used to produce complex components from a wide range of metals.
First introduced in the 1960’s, photochemical etching has revolutionized the way that metal components and parts are fabricated, providing a versatile and efficient solution to meet the demanding requirements of modern manufacturing.
As discussed in our other article, Chemical Etching: Everything You Need to Know, photochemical etching (PCE) has gained popularity for its exceptional efficiency, high precision, and rapid turnaround time. As a more resource-effective alternative to conventional methods such as laser cutting, water jet cutting, punching, and stamping, PCE not only streamlines the production process, but also allows for convenient modifications and adaptations throughout the manufacturing stage.
With a fast turn-around time, this etching process produces parts with exceptionally high dimensional tolerances, free from burrs, sharp edges, or need for further finishing.
What makes photochemical etching different?
Unlike traditional metal etching processes, photochemical etching is a subtractive machining process that uses photographic and chemical techniques to shape metal workpieces. Using a combination of chemicals and light, photochemical etching work and machining can produce intricate and complex designs on thin metal sheets with extreme accuracy and repeatability.
A major advantage of this etching process is its ability to produce precise parts that would be impossible or impractical to produce by traditional methods.
After the design image has been developed on the workpiece, a strong chemical solution is poured over the piece, selectively corroding unprotected areas and removing excess material. Photoresist imaging is used to select the areas to save or remove.
How does it work: the photochemical etching process
Chemical etching is a multi-step process that uses carefully formulated chemicals to create designs on flat metal sheets.
Due to the precision it delivers, highly complex and intricate designs can be produced on various metals. Despite its complexity, the process itself is fast and affordable, making it an excellent choice for metal prototyping and production.
The general process for chemical etching includes the following steps:
Photo Tooling
- The first step in metal preparation involves using CAD software to transfer an engineer’s digital drawing onto mylar film, which transposes the part images onto the metal.
Exposing
- During the chemical etching metal process, each sheet of metal is laminated with a photoresist film. Using the phototool, UV lamps expose the image of the part onto the photoresist coated substrate.
Coating
- It’s in this stage that clean, flat sheets of metal are coated with a polymer called photoresist. Applied to both sides of the coated metal sheet, the polymer is UV light sensitive and acid resistant. A vacuum seal is applied between the top and bottom layers of the phototool to seal in the coated sheet of metal.
Developing
- Using a developing machine, an alkaline solution is used on the sheets of metal to wash away the top and bottom film.
Etching
- The metal sheets are fed through an etcher that etches away the uncoated areas, leaving the precisely defined features of the part
Stripping
- To strip the mask from the metal surface, an alkaline solution is used. The etched sheets are dropped in a tank which removes the remaining photoresist film.
Forming
- In some cases, forming presses are used to bend the etched blank into precise three-dimensional shapes.
Inspection
- In order to ensure that your part meets your specifications, calibrated measuring instruments and state-of-the-art inspection machines are used. The part’s surfaces, dimensions and tolerances need to be inspected and approved during this final stage.
Common chemical etching applications
Boasting the benefits of speed, affordability and precision, chemical etching is the ideal process for components in a number of industries.
These include:
Aerospace: Photochemical etching is commonly used to produce parts that require high precision and accuracy, like fuel nozzles, heat exchangers, and engine blades.
Electronics: Due to its ability to create intricate patterns, photochemical etching is used to produce printed circuit boards (PCBs), which are used in almost all electronic devices.
Medical: With precision paramount to safety when it comes to the medical industry, photochemical etching is the preferred process for producing surgical instruments, implantable devices, and other medical equipment.
Automotive: With its precise and efficient process, photochemical etching is used to produce parts such as fuel injectors, brake components, gaskets, sensors and more
Microelectronics: Photochemical etching is widely used in the microelectronics industry to produce micro-components such as microcircuits, micro-electromechanical systems (MEMS), and microfluidic devices.
Photochemical etching: the ultimate etching solution
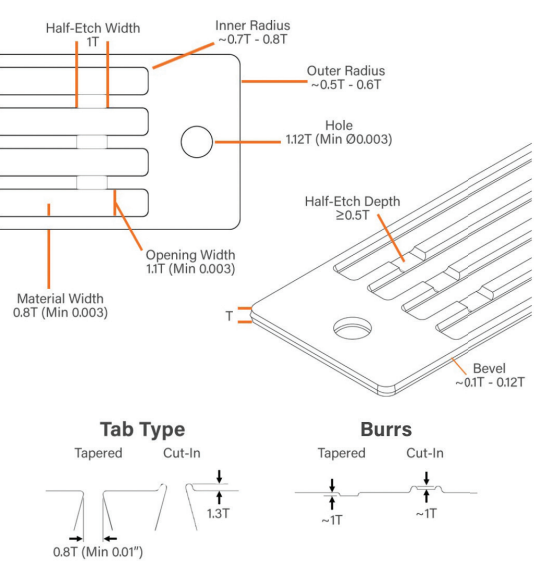
The photochemical etching process delivers a number of advantages over traditional metal fabrication techniques.
A major advantage of the photochemical machining or etching process is its high level of precision. This allows the production of specialized items or parts that are often impossible or impractical to produce by traditional methods due to being too thin or intricate.
In addition to its high degree of precision, you also benefit from fast turn-around times and low costs compared to other methods.
Let’s look at a real example: With photo chemical etching, a photo tool can be made quickly, can last the life of the part (if not longer), and can be reproducible, allowing for large production runs at reduced costs. This results in:
- Thousands of dollars saved with a photo tool compared to hard tooling methods
- A price not based on geometry
- The affordable production of complex and intricate parts
- The ability for low-cost, late design changes
- Prototype to production using the same process
Because photochemical etching uses chemical etchants and digitally produced designs to create a final item, photo tool costs are low compared to mechanical machining operations.
Additional advantages of photochemical etching include:
- Quick prototyping
- Rapid design modifications during mass production
- No burrs or sharp edges
- Hours-long turnaround time
Photochemical etching: how to choose the right company
At E-Fab, we use industry-leading equipment to turn a variety of metal alloys and composite materials into parts for a wide range of industries using chemical etching and various wet machining technologies.
Our innovative processes and expert staff ensure that every component we fabricate is of the highest quality.
Our areas of expertise include:
- Design/engineering assistance
- Material selection/metrology
- CNC machining (including micromachining)
- Lamination
- Heat treating
- Electro and electroless plating
- Joining (including welding, wire bonding, soldering, and braising)
Learn more about our photochemical etching capabilities here.