In this article, we break down the key differences between shield, waveguide, and angle forming processes so you can make an informed decision when selecting your manufacturing partners.
Metal forming plays a vital role in precision manufacturing, allowing manufacturers to create high-quality, cost-effective metal products with high design flexibility and consistency.
With multiple types of precision metal forming available, choosing the right process can profoundly impact the quality, efficiency, and success of your project.
But what are the differences between different forming processes, and how do they impact your precision metal products?
In this article, we break down the key differences between shield, waveguide, and angle forming processes so you can make an informed decision when selecting your manufacturing partners.
Before we explore the details of each manufacturing process, let’s start with a clear overview of the key differences between shield forming, waveguide forming, and angle forming. The following table concisely compares these processes, highlighting their primary functions, materials used, and typical applications across industries. This will serve as a quick reference guide as we discuss each process further.
Feature | Shield Forming | Waveguide Forming | Angle Forming |
Description | Involves shaping metal sheets or foils into enclosures for EMI and RFI protection of electronic devices. | Fabricates waveguides, hollow structures to guide electromagnetic waves efficiently with minimal loss. Used in telecommunications, radar systems, and more. | Utilizes bending or cornering techniques on metal pieces to achieve desired angles. |
Key Function | Protects sensitive electronic components from external electromagnetic disturbances and emissions from the components themselves. | Confines electromagnetic waves to direct them along a specific path, minimizing loss and interference. | Ensures precise bends or corners in metal components, crucial for the integrity and functionality. |
Materials Used | Nickel Silver, Brass, Copper, Steel (Tin-plated), Mu Metal (Permalloy, Hy-Mu 80). | Aluminum, Copper, Brass, Silver, Gold (for various types of waveguides). | Commonly uses materials like stainless steel and aluminum, shaped using bending, folding, and mitering. |
Industry Applications | Used in environments with sensitive electronic devices like data centers, hospitals (MRI facilities), and communication installations. | Essential in telecommunications, radar, medical devices (like MRIs), and microwave ovens, facilitating precise electromagnetic control. | Critical in aerospace for fuselage assemblies and wing structures; automotive for chassis and panels. |
Advantages | Provides effective EMI/RFI protection, enhances reliability and performance of electronic devices. Customizable to specific dimensions and requirements. | Offers low-loss transmission and frequency selectivity, ensuring efficient operation in targeted frequency bands. Provides additional shielding. | Provides high dimensional accuracy and consistency, crucial for high mechanical integrity applications. |
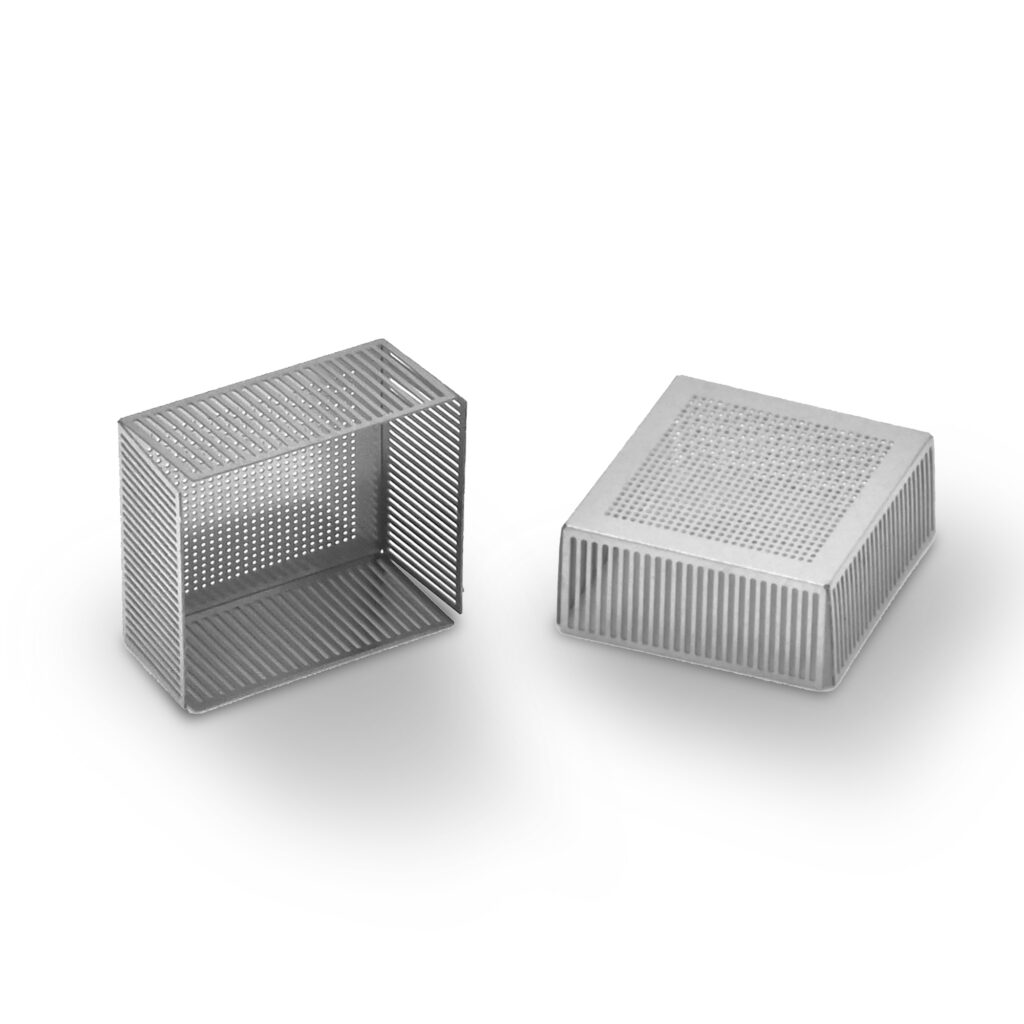
Shield Forming
Shield forming is a crucial process in precision metal manufacturing, especially for highly sensitive applications. It involves the shaping and manipulation of metal sheets or foils to fabricate shields that provide electromagnetic interference (EMI) and radio frequency interference (RFI) protection for sensitive electronic devices.
The primary role of shield forming is to create enclosures that safeguard electronic components from external electromagnetic disturbances and prevent emissions from the components themselves. These disturbances can come from a range of sources, from nearby electronic devices and radio signals to power lines. If they are not shielded properly, they can interfere with electronic equipment, resulting in performance degradation or equipment failure.
In shield forming, metal sheets or foil are typically stamped, bent, folded, and welded into intricate shapes that fit the dimensions of the electronic components or circuit boards they are designed to protect. The design of the shield is critical to ensure complete coverage and effective containment of electromagnetic emissions.
This type of forming uses a variety of materials, each offering unique properties suited to specific applications. Two of the most frequently employed materials are:
Nickel Silver: A blend of copper, nickel, and zinc, Nickel silver provides exceptional EMI shielding performance, working effectively across a wide frequency range, from mid-kHz up to the GHz range. Due to its inherent corrosion-resistant properties, it excels in environments where corrosion is a concern. The base material doesn’t require post-plating for corrosion resistance or solderability, and its permeability of 1 makes it ideal for applications like MRI facilities where magnetic materials are prohibited.
Brass: Brass is an incredibly versatile and widely available highly conductive alloy that is effective for shielding frequencies above 15 MHz. For effective shielding, you need to ensure the brass thickness is at least 0.002 inches (0.05 mm).
Copper: Copper is a reliable choice for EMI shielding due to its exceptional attenuation of magnetic and electrical waves. Because of its high conductivity, copper is used in diverse settings, from hospital MRI facilities to basic computer equipment. Like brass, it’s important to ensure a minimum thickness of 0.002 inches (0.05 mm) for optimal shielding.
Steel: Tin-plated steel is a cost-effective shielding solution that balances cost and performance. It works well from lower frequencies (kHz range) up to the lower GHz range. Tin plating also prevents rusting and offers a solderable surface for assembly. Carbon steel’s permeability provides low-frequency magnetic shielding absent in other materials.
Mu Metal (Permalloy or Hy-Mu 80): An alloy of nickel, iron, and molybdenum, Mu metal is commonly used in sensitive electronic devices, transformers, and magnetic shielding applications. Exhibiting extremely high magnetic permeability, it saturates at low magnetic fields, making it ideal for shielding against low-frequency magnetic interference.
Material selection in shield forming is crucial to ensuring optimal performance, longevity, and reliability of the electronic enclosures.
In addition to providing EMI and RFI protection, shield forming also contributes to the overall durability and mechanical integrity of the electronic enclosure. The shields are often designed to withstand harsh environmental conditions, enhancing the reliability and longevity of the electronic devices.
E-Fab leads the way in shield forming, precisely manufacturing materials into shields for use in highly sensitive applications. With advanced manufacturing capabilities and a focus on customization, E-Fab has built a reputation for producing custom enclosures tailored to specific dimensions and requirements.
E-Fab manufactures precision parts from many grades of stainless steel and high-quality aluminum RF shields, showcasing extensive expertise in working with a range of materials.
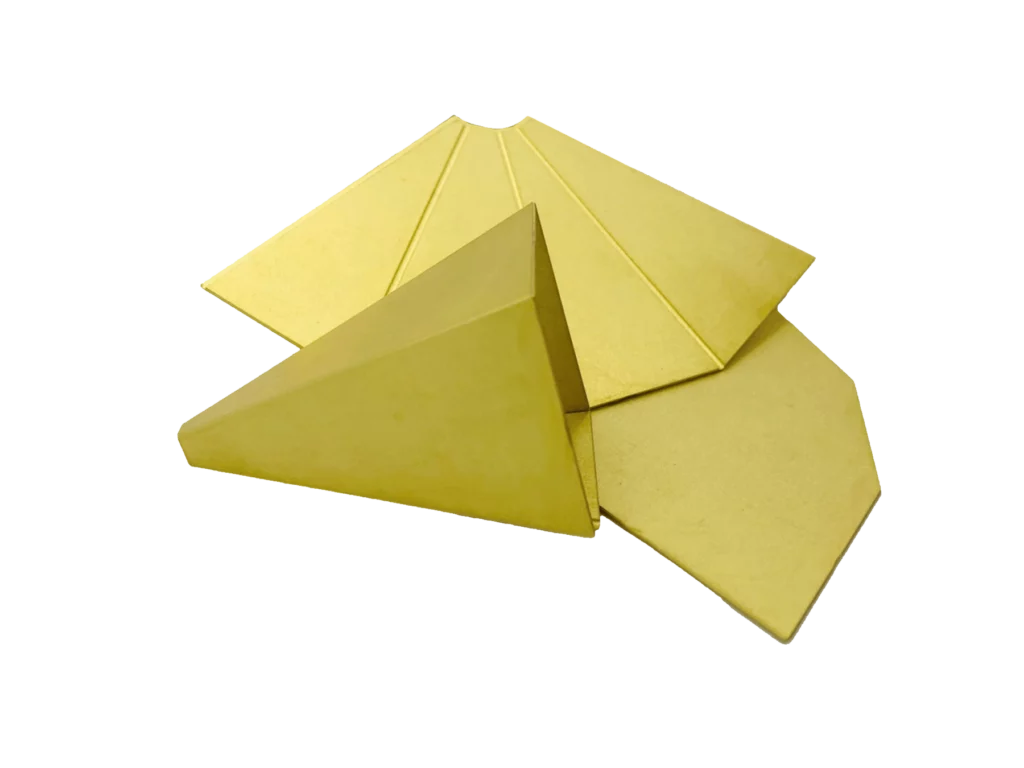
Waveguide Forming
Waveguide forming is a specialized process for fabricating waveguides, hollow structures designed to guide electromagnetic waves along a specific path. These structures are commonly used in various applications, such as telecommunications, radar systems, microwave ovens, and medical devices.
The concept of waveguides revolves around the principle of confining and directing electromagnetic waves through a physical structure, typically made of metal or dielectric material. Unlike transmission lines, waveguides confine electromagnetic waves within a bounded region, resulting in more efficient transmission with minimal loss.
The function of waveguides in guiding electromagnetic waves is crucial for several reasons:
- Confinement: Waveguides confine electromagnetic waves within their structure, preventing them from spreading out and dissipating into surrounding space. This confinement ensures that the energy of the waves is directed along a specific path, minimizing loss and interference.
- Low Loss Transmission: By guiding electromagnetic waves through a controlled medium, waveguides reduce the loss of signal strength that typically occurs in free space propagation. This enables the transmission of signals over longer distances with minimal attenuation.
- Frequency Selectivity: Based on their dimensions and geometry, waveguides can be designed to support specific frequencies or a range of frequencies. This frequency selectivity allows for the efficient transmission of signals within desired frequency bands while rejecting unwanted frequencies.
- Shielding: In addition to guiding electromagnetic waves, waveguides also provide shielding against external interference and environmental factors. The metallic walls of the waveguide prevent external electromagnetic fields from penetrating and disrupting the transmitted signals, ensuring reliable communication or operation of electronic devices.
Waveguide forming involves bending, welding, and machining to fabricate waveguide structures with precise dimensions and geometries tailored to the application. These waveguides facilitate efficient electromagnetic signal transmission in modern communication and technology systems with minimal loss and interference.
The choice of materials and geometries plays a crucial role in optimizing performance and efficiency in waveguide fabrication.
Rectangular waveguides: Characterized by their simple geometry and are commonly crafted from metals like aluminum, copper, or brass due to their excellent conductivity and ease of machining.
Circular waveguides: Often utilized in high-frequency applications and are typically fashioned from materials such as copper, silver, or gold for their superior electromagnetic properties and low signal loss.
Elliptical waveguides: Offer a balance between the characteristics of rectangular and circular counterparts, featuring a more complex geometry that requires precise machining techniques. They are commonly constructed from metals like stainless steel or aluminum for their durability and formability.
Each waveguide geometry presents unique challenges and opportunities in manufacturing, demanding meticulous attention to detail to achieve optimal performance in various applications.
The team at E-Fab is experts at forming the exact part from metal materials that work with existing components or detailed design specifications. We have proven experience in waveguide forming complex seamless structures to direct and control electromagnetic energy. Our precision manufacturing processes enable us to produce complex waveguide structures perfect for a range of applications across leading industries.
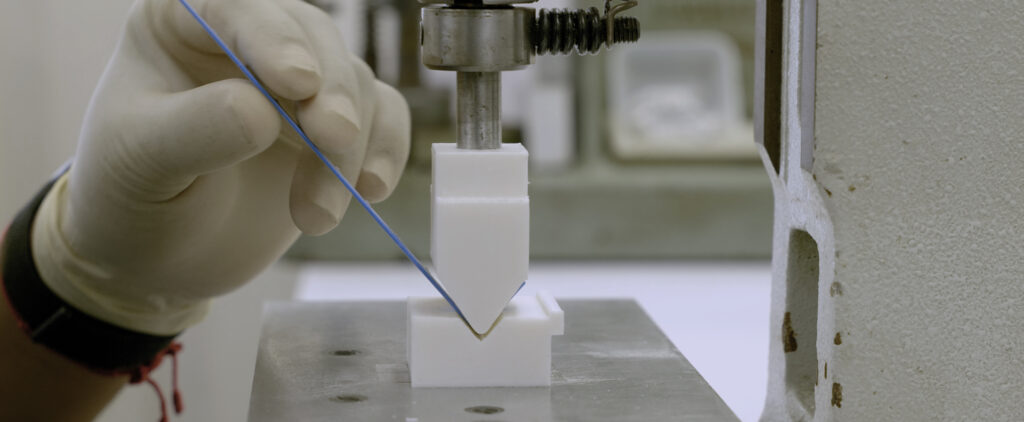
Angle Forming
Angle forming is used across a range of industries for creating precise bends or corners in metal components. Its precise process ensures dimensional accuracy and consistency, which is crucial for the integrity and functionality of the final product.
The angle forming process involves applying a force to a sheet metal piece, which bends at an angle and forms the desired shape. Angle forming is typically done with a press brake machine, and it plays a critical role in aerospace, automotive, and electronics applications.
The precision and reliability of angle-formed components are paramount across these industries, driving innovation and advancing technological capabilities in manufacturing processes and end products.
There are three primary methods commonly employed in the angle forming process: bending, folding, and mitering. Bending involves the use of specialized machinery to apply force gradually, shaping the metal along a linear axis to achieve the desired angle. Folding, on the other hand, utilizes a bending brake to crease the metal along a predetermined line, allowing for precise manipulation of angles. Mitering involves cutting two pieces of metal at an angle and joining them together seamlessly, commonly used in corners and joints for a clean finish.
The key applications of angle-formed components include:
Aerospace: Angle-formed components are integral to structural frameworks, providing strength and stability while minimizing weight. They’re used in fuselage assemblies, wing structures, and control surfaces, contributing to the overall aerodynamic efficiency and safety of aircraft.
Automotive: Angle-formed components are essential for chassis construction, body panels, and suspension systems, ensuring durability, rigidity, and crashworthiness.
Electronics: These components facilitate efficient heat dissipation, component protection, and compact device design by integrating enclosures, heat sinks, and mounting brackets.
Experts in angle forming, E-Fab is the trusted manufacturing team when maximum alloy strength is required for a part. With decades of experience serving a range of critical sectors, we’re uniquely positioned to provide innovative solutions and exceptional customer support for your angle forming projects.
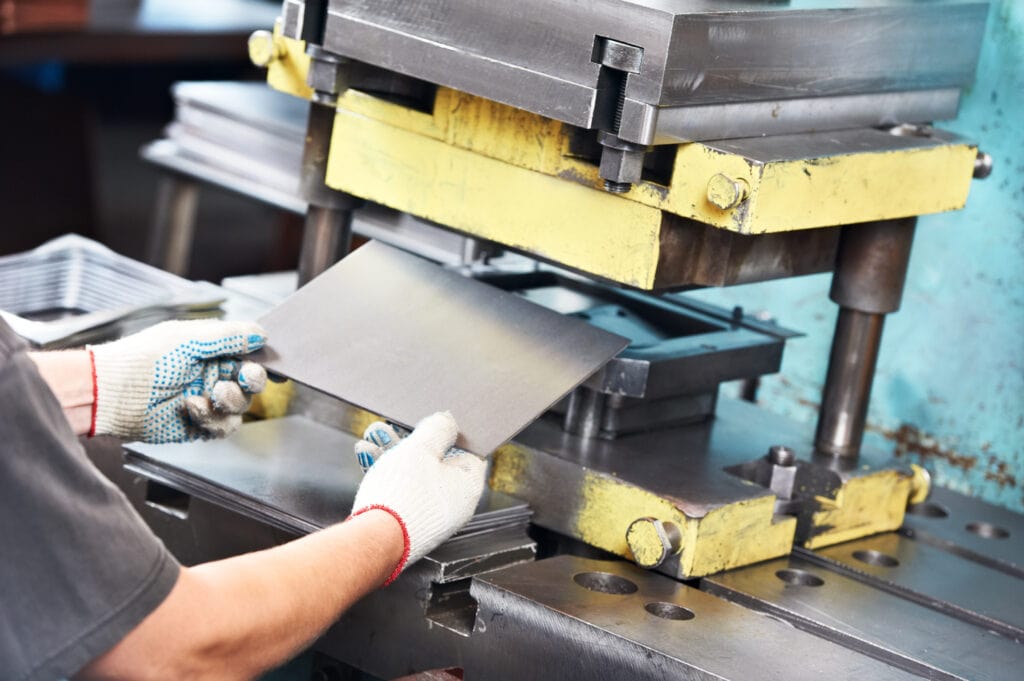
Proven Partners for Precision Metal Forming
Leaders in the metal forming industry, E-Fab produce high-quality, precise, and reliable components for shield, waveguide, and angle forming applications across diverse industries.
With our expertise in precision manufacturing, customization capabilities, and commitment to quality, we consistently deliver tailored solutions to meet the unique needs of each project.
By partnering with E-Fab, you can trust in our ability to ensure optimal performance and durability in even the most testing environments.
Our expert forming capability starts with CAD modeling by our engineering team. From there, our manufacturing floor, where engineers take machine code to form precise metal parts to exacting standards and specifications.
If you have a precision metal project that requires the highest quality forming, we can help.
We’d love to hear about your challenges and answer your questions.