Choosing the right photochemical etching manufacturer is crucial for quality and precision. This article guides you through the key factors to consider, helping you make an informed decision for your project’s success.
How to choose a photochemical etching manufacturer
Delivering exceptional efficiency, high precision, and rapid turnaround time, it’s easy to see why photochemical etching is quickly becoming the preferred process for industries that require accuracy and quality.
As a more resource-effective alternative to conventional methods such as laser cutting, water jet cutting, punching, and stamping, photochemical etching is behind the production of high-precision components for a range of industries, from aerospace and medical, right through to electronics and defense.
But, as photochemical etching’s popularity continues to rise, so does the number of manufacturers who claim to specialize in it. With quality and precision paramount, how do you choose a photochemical etching manufacturer you can trust?
In this article, we break down exactly what you need to look for in a manufacturer to ensure you receive the precision you require and the peace of mind you deserve.
Why Choose the Right Photochemical Etching Manufacturer?
When your industry relies on components with tight tolerances and complex geometries, you must work with a manufacturer with a proven track record of delivering the highest quality and precision parts.
By choosing the right manufacturer for your photochemical etching, you not only secure the integrity of your metal parts but streamline production processes, reduce waste, and ultimately enhance the quality and performance of your end products.
Due to the intricate and delicate nature of the photochemical machining process, you need to partner with a manufacturer with the expertise and precision to achieve exacting tolerances and intricate designs. A skilled manufacturer employs advanced techniques and state-of-the-art equipment, ensuring the utmost accuracy in producing metal components. In addition, a skilled manufacturer guarantees the highest level of precision and consistency through comprehensive quality control measures, from material selection to final inspection.
Leaders in the photochemical etching process and a member of the TPC network, E-Fab uses industry-leading equipment, innovative processes and expert staff to ensure that every component we fabricate is of the highest quality. As masters of photochemical machining, our commitment is to deliver precision metal parts ready to use in mission-critical applications. Our team of Quality Assurance professionals analyzes the parts we send out to ensure each meets technical specifications and precise requirements.
Key Considerations for Choosing a Photochemical Etching Manufacturer
When you’re selecting a metal etching manufacturer for precision metal components, several key considerations should guide your decision-making process:
Expertise and Experience:
Look for a manufacturer with a proven track record in photochemical etching. Expertise matters, especially when dealing with complex geometries and tight tolerances. An experienced manufacturer understands the nuances of the etching process, from design optimization to material selection.
Quality Control:
When it comes to precision metal manufacturing, quality is everything. Ensure the manufacturer follows rigorous quality control protocols at every stage of production. This includes material testing, process monitoring, and final inspection to maintain the highest standards of quality.
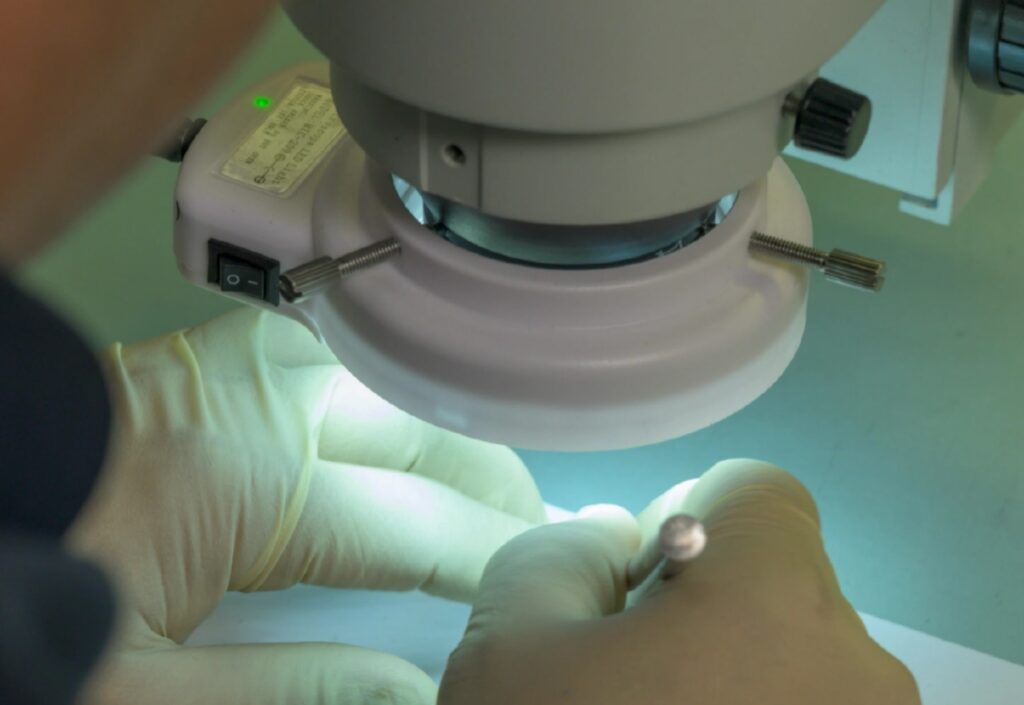
Production Capacity:
Assess the manufacturer’s production capacity to meet your project’s demands. Consider factors like batch size, scalability, and flexibility. A reliable manufacturer should be able to accommodate both small runs and large-scale production.
Technology and Equipment:
It’s important to evaluate the manufacturer’s technological capabilities, especially with such an intricate and delicate machining process. Look for manufacturers that use state-of-the-art equipment and advanced software in their process to ensure precise and consistent etching.
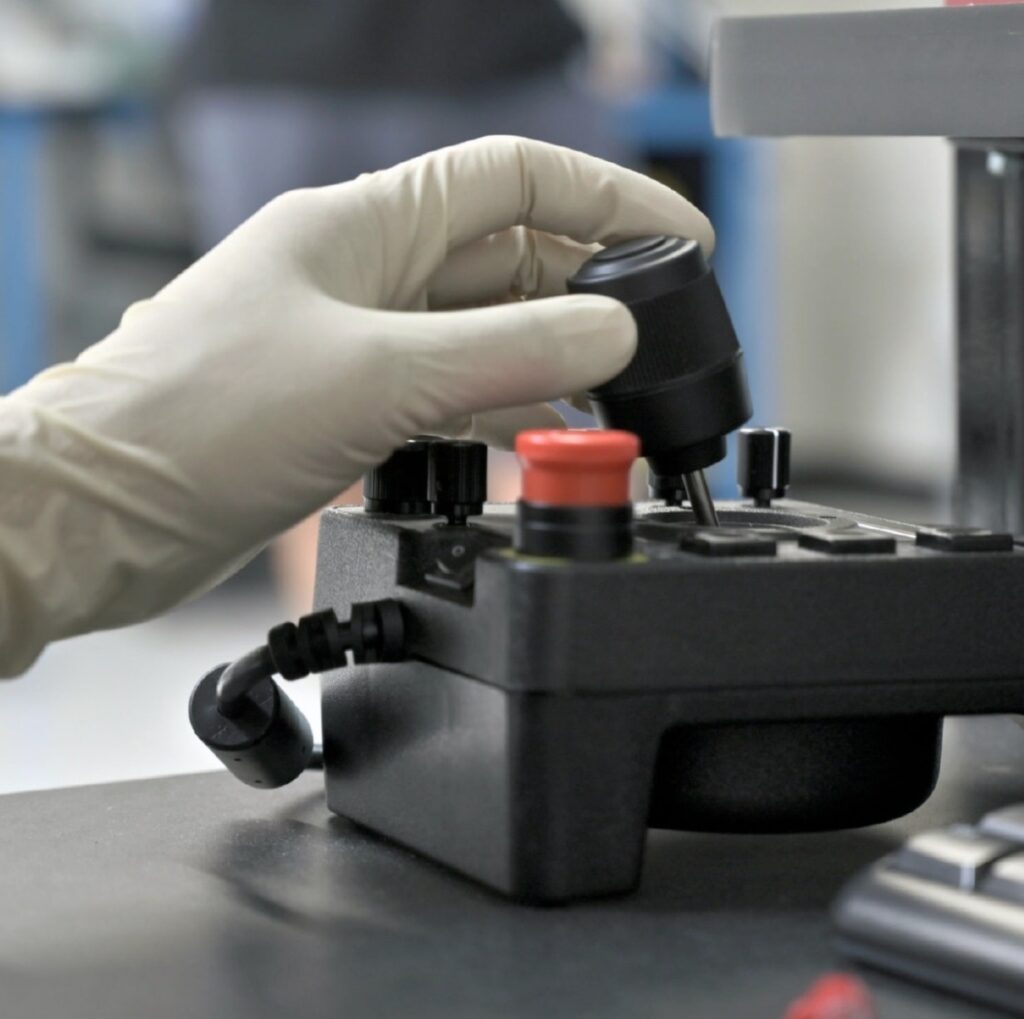
Lead Times:
Time-to-market can be crucial. Inquire about the manufacturer’s lead times and their ability to meet your project timelines. A manufacturer with efficient processes and well-managed workflow can help you reduce lead times.
Material Expertise:
Different metals and alloys require specific etching processes. Ensure the manufacturer has expertise in working with the materials relevant to your project, whether it’s stainless steel, titanium, or other specialty metals.
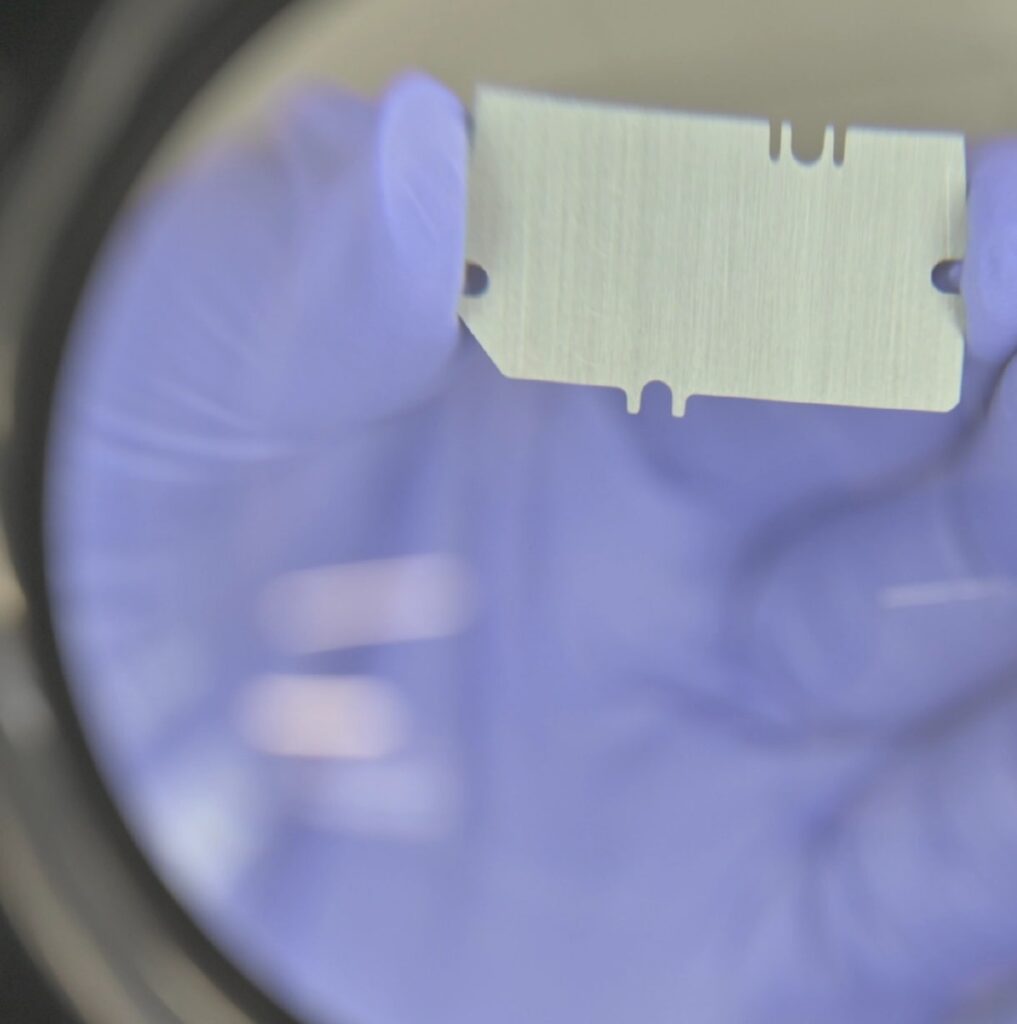
Cost-effectiveness:
While cost is a significant factor, it should not be the sole determinant. Consider the overall value offered by the manufacturer. A slightly higher upfront cost may be justified if it ensures superior quality, shorter lead times, and fewer post-production issues.
References and Reputation:
Research the manufacturer’s reputation in the industry. Seek references from past clients and review case studies to gauge their performance and reliability.
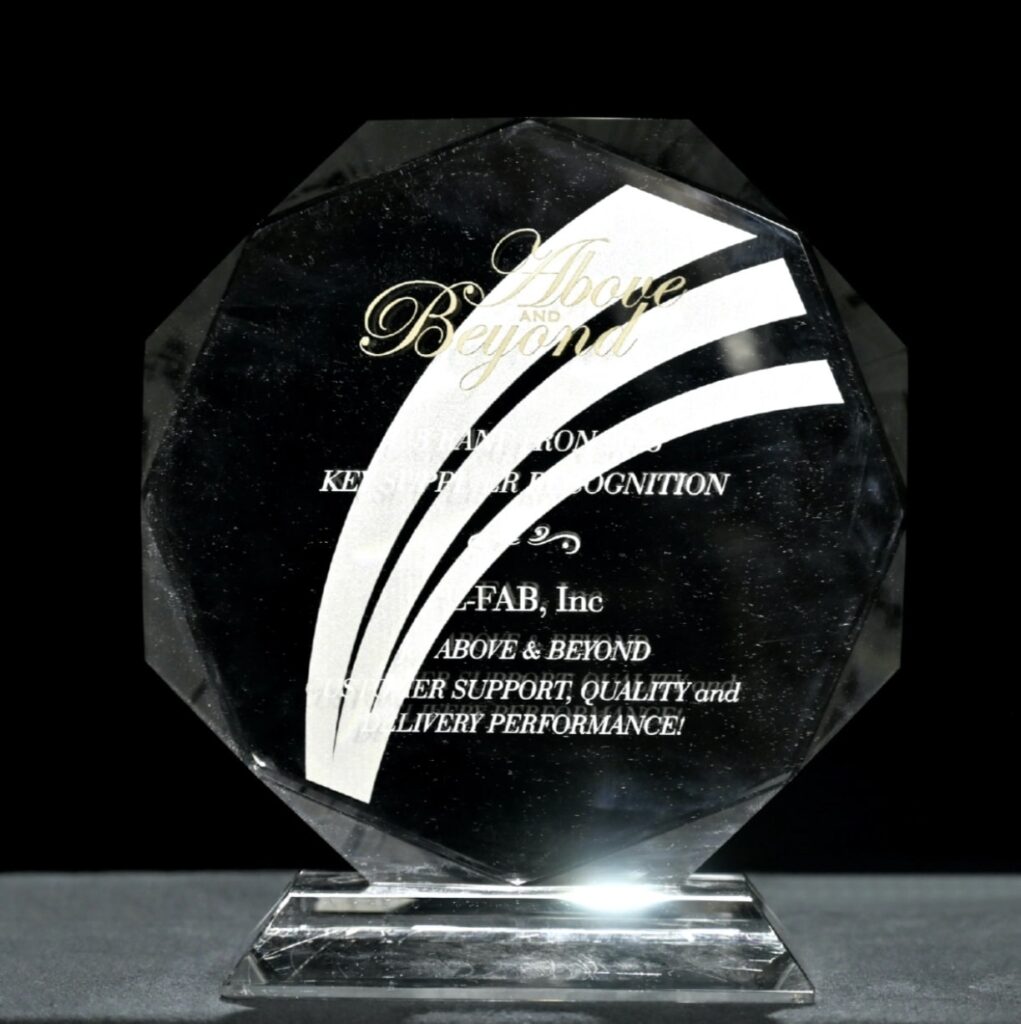
Communication and Collaboration:
Effective communication is crucial for project success. Choose a manufacturer that values collaboration, listens to your needs, and provides transparent updates throughout the production process.
By carefully considering these factors, you can choose a photochemical etching manufacturer that not only meets your immediate project requirements but also establishes a long-term partnership for precision metal manufacturing.
What Sets E-FAB Apart - Photochemical machining experts
As the trusted partner for photochemical etching, E-Fab is where ingenuity meets precision. Our engineers, manufacturers, and quality assurance specialists turn ideas into precision parts through collaboration, engineering, and our expert etching process.
As a proud member of The Partner Companies group of specialty manufacturers, we share a commitment to excellence, precision, and innovation, serving the defense, aerospace, medical, telecommunications, semiconductor, and renewable energy industries.
The preferred provider for leading industries across the country, our stats speak for themselves:
• 95% on-time delivery rate
• Less than 1% reject rate
Quality, reliable production is just the start. Our secret is in our strict quality control.
We’re committed to quality and customer satisfaction, which is why our team of Quality Assurance professionals analyzes the parts we send out to ensure each meets technical specifications and precise requirements.
With safety, satisfaction and business success reliant on the quality of parts delivered, we utilize the latest technology to check parts down to the micron. This includes an OGP® SmartScope with a 12:1 AccuCentric Zoom Lens, Keyence optical measurement system, and advanced software for detailed inspection.
Case Studies or Customer Testimonials
Case Study Headline
Heat treating plays a pivotal role in the precision forming process, responsible for improving the performance and durability of precision-formed metal components. By subjecting the formed metal to controlled heating and cooling cycles, mechanical properties such as hardness, strength, and ductility are enhanced – improving wear resistance and fatigue strength. Through processes like annealing, quenching, and tempering, heat treating relieves internal stresses accumulated during forming, mitigates distortion and refines the material’s grain structure for optimal resilience.
Case Study Headline
A fundamental technique within the precision forming process, bending is used to shape metal materials to exacting specifications. With its role extending beyond just changing the shape of the metal, bending is a conduit for achieving intricate geometries and angular precision crucial for component functionality. Manufacturers can bend metal with remarkable accuracy by skillfully applying controlled force through methods like press brake forming, crafting complex shapes that traditional methods would struggle to replicate. This process ensures that components align seamlessly within larger assemblies and minimizes the need for post-processing adjustments, saving valuable time and resources.
Choosing the right company for your photo etching
Partnering with a reliable photo etching partner delivers more than just precision; it translates into enhanced product performance, reduced lead times, and cost savings, making it a strategic investment for any customer needing precision metal components.
If you’re looking for a reliable partner for your photochemical etching, the team at E-Fab are here to help. We use industry-leading photochemical machining equipment to turn a variety of metal alloys and composite materials into parts for a wide range of industries using chemical etching and various wet machining technologies. Our innovative processes and expert staff ensure that every component we fabricate is of the highest quality.
Our Photo Etching areas of expertise include:
- Design/engineering assistance
- Material selection/metrology
- CNC machining
- Lamination
- Heat treating
- Electro and electroless plating