In this article, we look at the advantages of photochemical etching, the parts it can produce, and the reasons why it’s shaping the future of precision manufacturing.
In the dynamic landscape of precision manufacturing, more and more industries are demanding high-efficiency, custom-made components for a range of critical applications.
With its ability to produce complex features and micro-sized components with exceptional accuracy and repeatability, photochemical etching is delivering a modern solution for industries where precision, accuracy, and performance are paramount.
Renowned for our expertise in photochemical etching, E-Fab has consistently delivered exceptional results to industries requiring intricate, high-quality metal components. Led by our advanced photochemical machining process, capable of achieving extremely difficult requirements by tightly controlling every aspect of our process, we consistently produce industry-best parts and components.
In this article, we look at the advantages of photochemical etching, the parts it can produce, and the reasons why it’s shaping the future of precision manufacturing.
Understanding Photochemical Etching
Photochemical etching, also known as photochemical machining (PCM) or chemical milling, is a highly precise, cost-effective metal machining process used to produce complex components from a wide range of metals.
The intricate process removes selective areas of the metal sheet using chemical etchants. First, a light-sensitive photoresist is applied to the metal surface first. A detailed pattern of the desired part is then transferred onto the photoresist through photolithography. When exposed to light, photoresist hardens, protecting some areas while leaving others exposed. Chemical etchants are then applied to dissolve the unprotected metal, leaving behind the precise and intricate shape of the component.
With its ability to produce complex, burr-free, and highly consistent parts, photochemical etching has quickly become the preferred method in industries requiring intricate metalwork, such as aerospace, electronics, and medical device manufacturing.
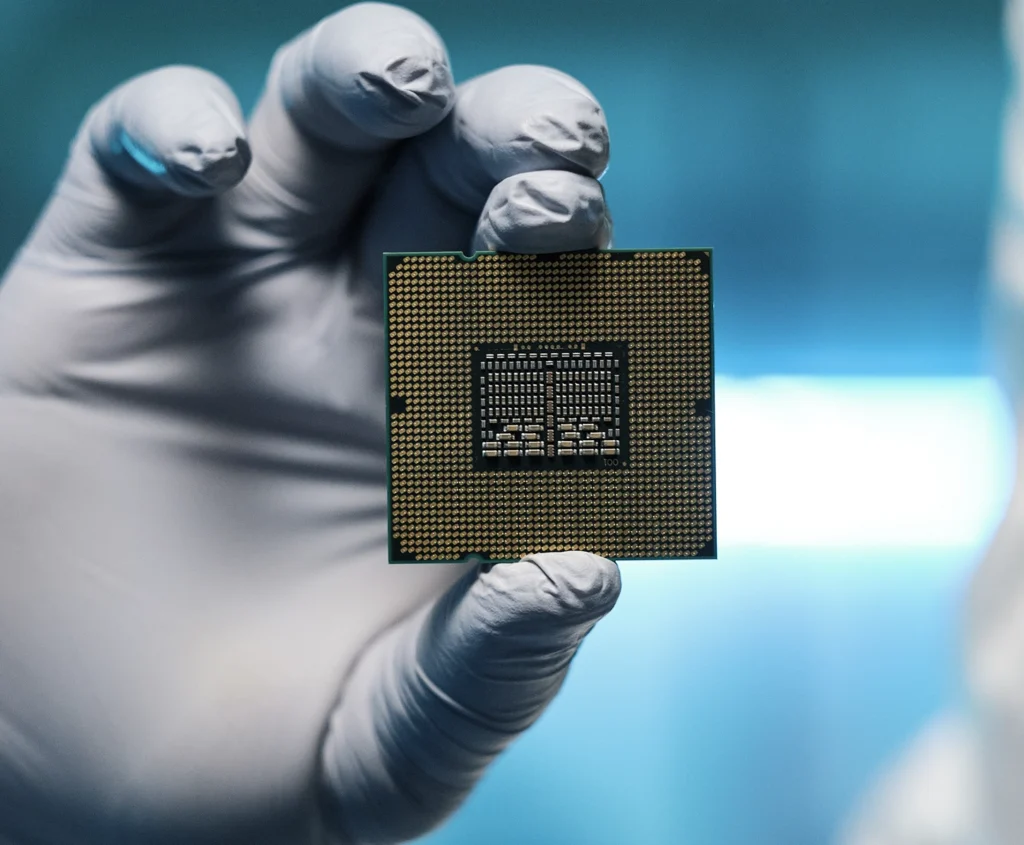
Photochemical Etching Applications in Action
Fast, repeatable, and cost-effective, with shorter lead times than other metal fabrication methods, the chemical etching process is widely used for producing high-precision components across many industries and applications.
For industries that demand finely detailed metal components with exceptional precision, photochemical etching has become a cornerstone. One primary industry heavily reliant on this process is aerospace, where lightweight and carefully designed parts are critical for aircraft performance. The electronics industry also heavily relies on photochemical etching to produce precise components like connectors, contacts, and microcircuits. In the medical sector, photochemical etching is meeting the demand for miniaturized and complex components in devices such as implantable devices and surgical instruments, while the automotive industry utilizes this process to produce precision parts like fuel injector nozzles and sensors.
Some of the key parts delivered by photochemical etching include:
- Optical Apertures
- Heat exchanger plates
- Bipolar plates
- RF shields, lids & carriers
- Optical encoders
- Lead frames
- Aerospace components, including EMI/RFI Shielding, Wire Mesh and Stabilization Shims, Covers, Lids, and Heat Sinks
- Waveguide
- RF Microstrip contact
- Medical Components, including surgical instruments, stents, and orthopedic bone implants
- Radiation shields
- Mesh for current collectors
- Filters and screens
- Foil bearings
As a leader in photochemical etching, E-Fab’s chemically etched parts are used in a wide range of applications that include:
Bipolar Plates for Fuel Cells and Electrolyzers
Using our advanced chemical etching process, we manufacture photochemically etched custom bipolar flow field plates or fuel cell plates etched with corrugated channels.
Delivering faster lead times, we have the flexibility to create complex, high-performance bipolar plates.
Custom Meshes & Screens
Our etched mesh screens are used in a variety of applications, including medical devices, particle filters, and current collectors.
Unlike traditional woven meshes, our advanced process allows us to produce meshes and screens with more complex geometry, higher accuracy, and greater integrity.
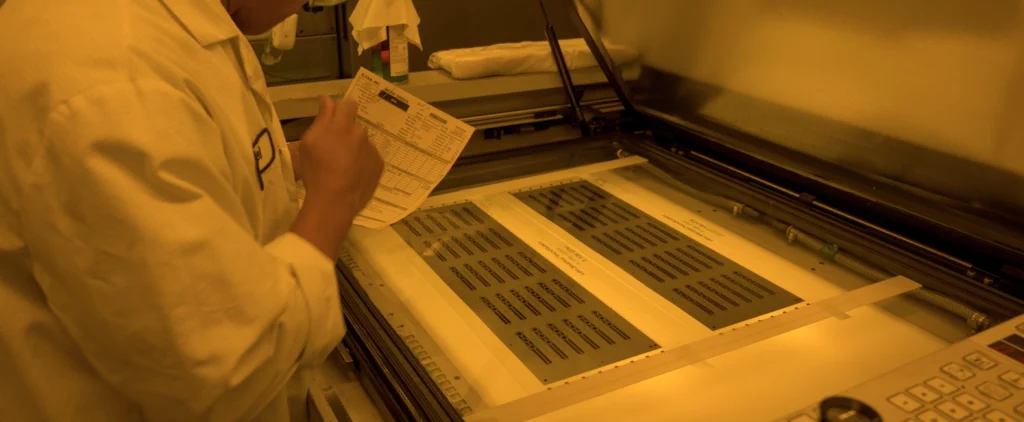
The main advantages of Photochemical Etching
Boasting several benefits compared to traditional machining processes, photochemical etching has become the preferred method for the production of highly detailed components for leading industries across the globe.
Providing exceptional precision and accuracy, it creates finely detailed metal parts with tight tolerances and delivers enhanced component integrity by minimizing stress on the material and ensuring burr-free edges.
Its ability to create complex geometries and microstructures with uniform precision ensures that each component meets stringent specifications.
Key advantages of photochemical etching include:
Competitive cost
Whether producing a few prototypes or larger quantities, photochemical etching offers cost-effective production without the need for expensive tooling or setup, making it ideal for both small-scale and large-scale projects.
Fast turnaround
The rapid production cycle of photochemical etching ensures customers receive their parts promptly, facilitating on-time project completion and accommodating design adjustments.
Burr-free, stress-free parts
Unlike traditional mechanical processes, such as stamping or milling, photochemical etching eliminates the formation of burrs – undesirable raised edges that can compromise component integrity. The use of chemicals also removes mechanical force from the process, resulting in stress-free parts with smooth edges.
Low-cost tooling
Photochemical etching allows for the direct transfer of digital designs onto the metal surface, eliminating the need for expensive and time-consuming tooling setups and reducing both production costs and lead times.
Metallurgical properties preserved
The chemical nature of the etching process is inherently gentle, which allows for the
retention of original grain structures, hardness, and other metallurgical characteristics of the metal. The components produced exhibit consistent and reliable material properties.
Design flexibility
The chemical etching process easily allows for the customization of designs so you can experiment with various shapes and sizes without incurring significant setup costs. Using digital files as tooling, you have the flexibility to make design changes quickly and cost-effectively.
Wide range of materials
The photochemical etching process works on a variety of materials, including various metal grades, giving manufacturers the freedom to choose materials that best suit the applications’ functionality and desired performance.
Dimensional repeatability
This precise etching process allows for the accurate reproduction of intricate designs with tight tolerances, ensuring consistent and precise dimensions across multiple parts.
Precise and complex geometries
Photo chemical etching achieves unparalleled precision, creating incredibly detailed and accurate parts with intricate features and complex geometries.
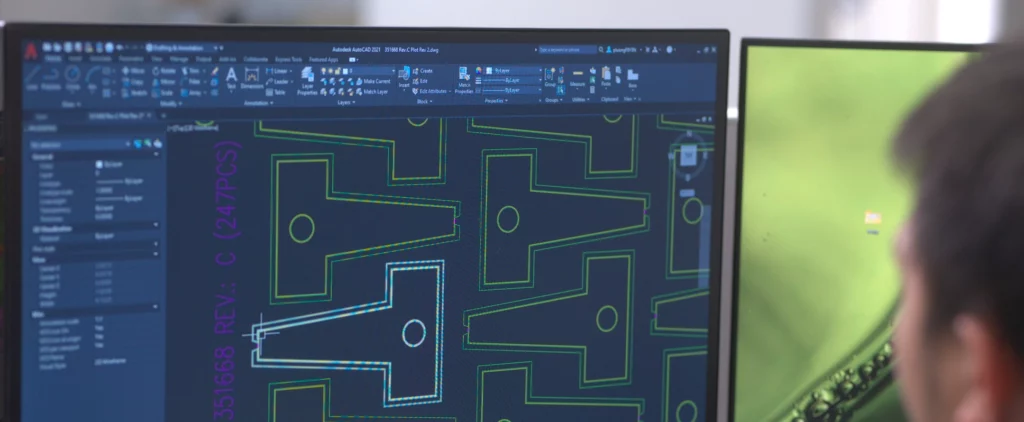
E-Fab's Proven Etching Process
E-Fab’s photochemical etching process has been developed from years of experience in creating high-precision metal parts. Led by our in-house experts, we consistently produce finer geometries with greater precision than the industry standard. We are AS9100D-certified, ISO 9001:2015-certified, ITAR-registered, and RoHS-compliant, so you can rely on us for high-quality production.
Our proven multi-step process involves:
- Design Evaluation/Engineering for Manufacturability
Before beginning the chemical etching process, our expert engineering team works directly with the customer to ensure their precision metal parts’ smooth and successful production. This includes using software such as AutoCAD to generate a repeating pattern from a customer file, which is then printed onto mylar film.
- Material Selection
We start our chemical etching process by selecting the appropriate metal from a wide range of available materials.
Depending on the application of the metal parts, our team works closely with you to choose the right material based on its specific functional properties.
The most commonly used materials for chemical etching include stainless steel, copper and its alloys, nickel (or its alloys), and aluminum.
- Metal Sheet Metal Lamination
A dilute acid solution is used to clean the metal sheet once the material is chosen. After that, we laminate the metal sheet with a UV-sensitive dry film photoresist that acts as a mask, preventing the chemical etchant from coming into contact with areas of the metal that need to be retained for the correct geometry.
The photoresist must be well-bonded to the metal sheet to ensure accurate reproduction of the desired shape or pattern.
- Digital Design
By using a UV laser digital imaging tool, the design is transferred to the photoresist laminated on the metal sheet from a digital image. Photoresist film can be applied on both sides of the metal sheet, and different designs can be etched.
After the imager transfers the design to the metal sheet, the photoresist is developed, which removes the exposed resist. We are now ready to etch the sheet.
View our Design Guidelines here for dimension and tolerance parameters.
- Etch Design
Our etchers spray a chemical etchant, usually ferric chloride, simultaneously on both sides of the patterned sheet. High pressure is used to spray, etching away all unprotected material.
The final etched components are revealed after removing the remaining photoresist from the sheet.
Our skilled technicians and state-of-the-art machines meticulously control the time and the amount of etchant used for this process. They consider several factors, such as the type of metal and the size and thickness of the metal sheet. Perfected etch times guarantee etched parts that exceed your applications’ requirements.
- All-Encompassing Turnkey Solutions
E-Fab specializes in joining metal parts with precision. We use a technique called thermocompression bonding. This method uses heat and pressure to bond parts together, ideal for making complex 3D structures from 2D etched components. It’s great for products that need to be strong and conduct electricity well, like in electronics and tech fields.
After bonding, we also focus on making these parts last longer and perform better with our finishing services. We offer various plating options like anodizing, gold plating, and more to protect and enhance your parts. Our finishing touches, such as electropolishing and passivation, ensure your components look good and meet high-quality standards.
- Quality Control
Following the removal of the photoresist layer (either manually or with a stripping machine), parts are rinsed before being separated. The individual parts etched on each sheet can be separated or left with tabs on the sheet.
We recommend tabbing to allow for faster inspection and safer handling during and after production. For this, a tab is connected to the individual parts so that they stay on the sheet for easy removal after manufacturing is complete.
During the chemical metal etching process, our quality inspectors review and check each part to ensure it meets the dimensional requirements and tolerances specified at the design stage.

Shaping the Future of Precision Manufacturing
Photochemical etching is experiencing a surge in innovation, paving the way for exciting trends and future advancements. One notable trend is the increasing adoption of digital technologies in the design and control of the etching process. Computer-aided design (CAD) systems are becoming more sophisticated, enabling manufacturers to create intricate and complex designs that push the boundaries of traditional capabilities. Additionally, the integration of artificial intelligence (AI) and machine learning in process optimization is enhancing efficiency and precision.
Miniaturization trends in various industries are driving the demand for even finer features, and photochemical etching is well-poised to meet these requirements. The continuous exploration of new materials and the development of eco-friendly etchants are also contributing to the evolution of this technique.
Photochemical etching has the potential for further innovation as the industry embraces Industry 4.0 principles, promising a future where precision metal manufacturing pushes the boundaries of technology and design. With the integration of advanced technologies such as automation, data analytics, and smart manufacturing systems, photochemical etching processes can become more streamlined, efficient, and responsive to dynamic production demands. The digital connectivity inherent in Industry 4.0 also enables real-time monitoring and control of the photochemical etching process, optimizing precision and minimizing material waste.
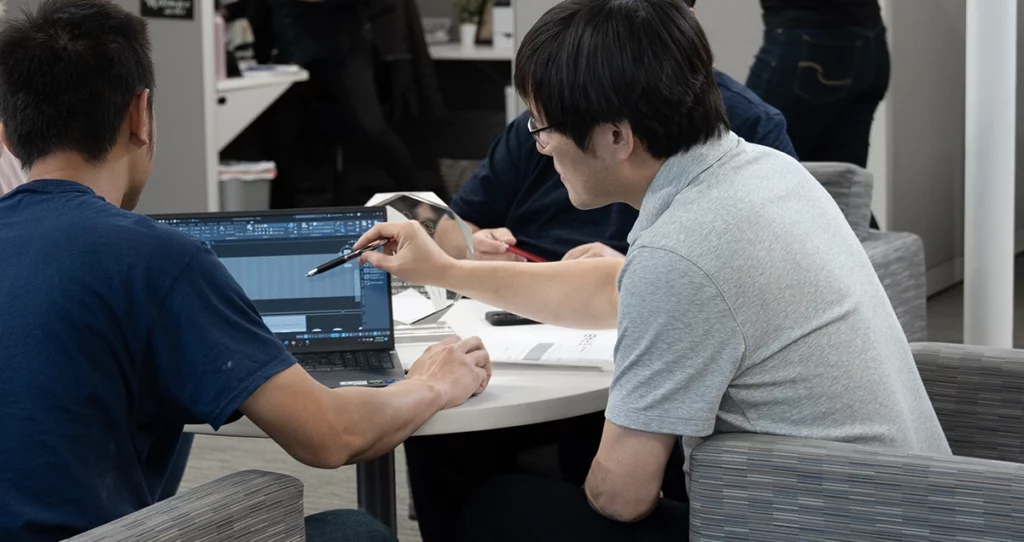
A Proven Partner For Precision Photochemical Etching
As more and more industries demand precise, intricate components, photochemical etching has become the preferred process due to its high precision, fast turnaround, and low-cost tooling. A cheaper alternative to traditional methods like laser cutting, water jet cutting, punching, and stamping, it also offers the added benefit of easily making changes and adjustments during production.
With a fast turn-around time, this etching process produces parts with exceptionally high dimensional tolerances, free from burrs, sharp edges, or the need for further finishing.
Here at E-Fab, we’ve manufactured the highest-quality precision components and assemblies specifically designed for mission-critical applications, and we’ve done it for over 40 years. We are committed to delivering best-in-class components at quick turnaround times using our advanced chemical etching process for metal parts.
Working with a wide range of partners from aerospace and defense to biomedical and renewable energy, we take your product from design and concept to prototyping through full production with fast and reliable delivery.
If you’re searching for a proven photochemical etching partner, our team is here and ready to start talking, whatever your application may be.